脱炭素、脱プラスチックの推進が急務となる昨今、まだ使える廃プラスチックをできるだけ再利用し、石油から作られたバージンプラスチックを削減していくことが重要なのは疑いようがなく、再生プラ原料の安定確保は各メーカーにとって大きな課題になってくるでしょう。そんな中、国内で発生した廃プラスチックを国内で加工し、100%国内再生原料で作る再生ごみ袋を紹介します。
今回は、国内で発生した廃プラ100%の再生ごみ袋を作る大阪和田化学工業㈱と、その原料を作る亜星商事㈱のインタビューを元に、再生ごみ袋ができるまでをご紹介します。
※今回の記事は大阪和田化学工業㈱のメディアサイトより許可を得て一部変更のうえ転載しています。※旧サイト(環境と人)からの転載記事です。
再生プラ原料の仕入れは世界規模での関心事
各国でプラスチックの使用削減が進んでいます。特に欧州では各国とも独自の削減目標を掲げ、身近な消費財にまで再生プラスチックが活用されています。ヨーロッパのスーパーへ行けば、灰色がかった容器の日用品を目にするでしょう。
一方、日本では高い衛生基準が影響し、口に入れる食品に関わるパッケージだけでなく、洗剤ボトルなどの容器包装に対しても透明感のあるバージンプラが歓迎される傾向があります。
生活者としてはきれいなボトルを使えるメリットがありますが、その反面、使い捨ての商品にバージンプラを使うのは環境面はもちろん、コスト面でもどんどん不利になると予想されます。なかでも、私たちが日常的に使っている「ごみ袋」は中身と一緒に燃やされるためにあると言っても過言ではないのですから、そこにバージンのプラスチックを投入するのは非常に勿体ないと言えるでしょう。
そのため、バージン原料でなく再生原料でごみ袋を作る流れになるのは必然と言えますが、そうすると今度は原料の安定確保が問題となってきます。
再生プラの原料の多くは人件費の安い国から輸入されますが、世界動向を見ると、欧州はじめ脱炭素の具体的目標を掲げる各国ではすでに再生原料が不足しつつあり、東南アジアや中国の会社からペレットをこぞって買い、現地リサイクル企業の買収を始めています。その結果、日本が買い負けて商品が作れなくなるリスクがあるのです。
国内循環するごみ袋
こうした難しい状況の中、国内で発生した物流用のストレッチフィルム廃材を原料に、国内で製造販売しているのが大阪和田化学工業㈱の「進化するごみ袋」です。
物流の現場においてダンボールに並ぶほど欠かせない梱包資材であるストレッチフィルムは、リサイクルの対象として優れています。特に空港や港湾では365日休みなく海外から大量の物資とともにストレッチフィルムが入ってくるので、そのまま国内で再利用するのは非常に理に適っています。
廃材を途上国へ輸出して加工するプロセスがないため、輸送にかかるコストやCO2排出を抑えることが可能な上、先に述べたようなグローバルリスクの心配がないため安定的な供給が可能で、まさに持続可能なごみ袋と言えるでしょう。
この進化するごみ袋がどのように作られているのか、亜星商事㈱の工場での再生ペレット化と、大阪和田化学工業㈱の工場でのごみ袋の製造までの一連の流れを見ていきましょう。
再生ごみ袋ができるまで1:廃ストレッチから再生ペレットまで
まずは搬入に来たトラックから降ろしたプレス(圧縮した塊)を屋内に保管します。
この時、汚れが目立つものは洗浄工程を挟みますが、進化するごみ袋に使われる原料は元々洗浄がいらない高品質なものです。

加工するために倉庫から加工場に運び、そこでプレスを開梱して、手選別を行います。

常時2名ほどの作業員による手作業で、挟まった紙、マジックペンの汚れ、フィルム以外の大きな異物、それにストレッチフィルム以外のプラ、HDPEだったりPPも除きますし、PVC(塩ビ)は厳しく取り除くようにしています。

それらを手作業であらかた除いた後はコンベアに乗せると押し出し機に投入され、手作業で除ききれないモノがメッシュで取り除かれます。

最後に粒状にカッティングされ、冷却・脱水し、ふるい機にかけて、きちんと一粒一粒分かれているペレットだけがフレコンバッグに詰められていきます。

こうして、使用済フィルムからペレットという原料の状態にまで戻され、進化するごみ袋の製造工場まで運ばれていきます。

再生ごみ袋ができるまで2:再生ペレットがごみ袋になるまで
こうして廃ストレッチフィルムから粒状に加工された再生ペレットが、大阪和田化学工業㈱の製造工場に運ばれます。
再生ペレットを再び熱で溶かし、薄く広げます。そこで綿あめ機のような機械で空気を吹き込み、風船のようにインフレーション(膨張)させ、袋状に加工します。
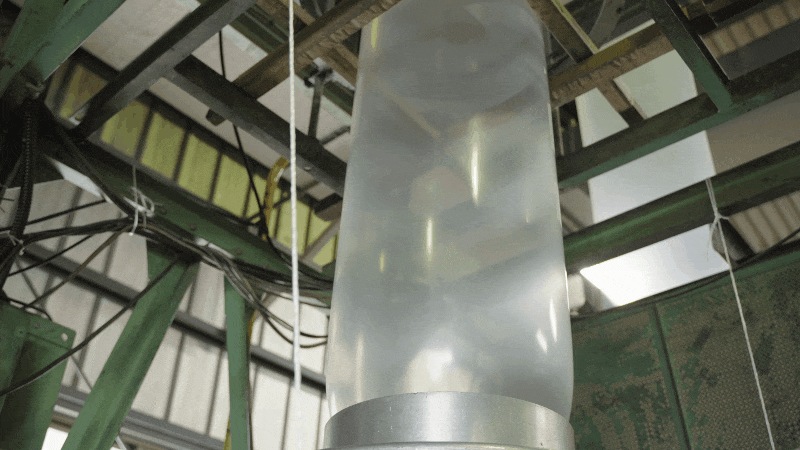
それを上部で折りたたみ、表面に印刷を入れたら、袋の長さに合わせて底の部分を熱溶着してカットします。

こうして出来上がった進化するごみ袋は、100%再生ストレッチフィルムを使うことで、環境に配慮したごみ袋です。具体的なCO2の削減数値が試算されており、メディアサイトで公開されています。
そして、ストレッチフィルム由来のため非常に伸縮性が高く破れにくい特徴を持っているため、再生ごみ袋にありがちな破れやすいといった強度の心配がないこともメリットです。

進化するごみ袋の原料である再生ペレットを卸している、亜星商事㈱ 取締役副社長 仲澤拓海 氏よりお話を伺いました。
亜星商事(株)インタビュー

ーまずは会社の概要について教えてください。
私たち亜星商事は、ポストコンシューマ材由来の廃プラスチックのリサイクルをする再生原料メーカーです。2種類の樹脂(PP/PE)、その中でも物流梱包資材を主に扱います。廃ストレッチフィルム、PPバンド、あとはペットボトルキャップも梱包資材に含まれます。他にはプラスチックパレットやタンク類も含めた物流系の資材を主に扱って、大体700t/月くらいの再生プラスチックを作っています。
その内、廃ストレッチフィルムは月に約150〜200tくらいペレット化して販売させていただいています。進化するごみ袋に使っていただいている原料も、弊社が提供しております。
ー廃ストレッチフィルム原料は主にどこから仕入れていますか?
廃ストレッチフィルムの排出元は様々です。毎月プレス20本を納める排出元さんから、貯めに貯めて半年に1回みたいな排出元さんもいます。全て合わせると100社前後でしょうか。
最も量が多いのは古紙屋さんからです。彼らがダンボールと一緒に廃ストレッチフィルムを回収しているケースが多く、あとは産廃屋さんはもちろん、場合によってはメーカーさんから直接頂く場合もあります。メーカーさんが自社で小型のプレス機を買って圧縮までして、弊社に持ってきてくれる所もあります。
ー国内原料を国内向けに再生するというのは珍しいですか?
今でこそ珍しくなくなってきていますが、その中でも大阪和田化学さんは先駆けだったんじゃないかと思います。
もともと弊社は1998年の創業から2017年まで日本で廃プラを集め、中国の工場で再生ペレットを作っていました。ですが2018年から中国への廃プラ輸入が禁止になったので、今いるこの笠間市の拠点を生産工場ラインにして国内でのペレット製造を開始し、5年目になります。

そんな流れから海外への販売が特に多かったという事情もあり、2018年にこの工場がスタートした時は、海外輸出95%、国内販売5%くらいのスタートでしたが、2023年12月現在は輸出が55%、国内が45%くらいにまで国内消費が増えました。
今思うと、そのきっかけは大阪和田化学さんだったと思います。正直な話、海外とくにアジア諸国に売れば、品質が多少悪くても何とかなるのでラクではありましたが、もともと我々としても国内で集めたものは国内に還元したいっていう思いがあったので、国内に再生拠点を置いた機に色々やりたいと考えていました。
そんな折に大阪和田化学さんとお仕事をする機会を得たりして、徐々に国内で流通させるアイテムが増えてきました。
サプライチェーンの距離感が近いので、トレーサビリティを取る仕組みを整えたりとか、まぁ問題ないだろうと思っていたロットに対して、一部だけ品質基準に足りなかったら返品してくれればいいよ、みたいな柔軟なやり取りができたりと、これまでの海外との商売の仕方とは違うような形でスタートができましたね。

ー品質基準はやはり海外よりも厳しくなりましたか?
そうですね。でも大阪和田化学さんは、非常に使いこなしてる会社だと思います。
ー使いこなす、ですか?
このメッシュ数じゃ駄目だとか、この色じゃ駄目だとか、ペレットの納品に際して他社さんだと色んな基準があるんですが、大阪和田化学さんはその基準が他社よりも緩いです。それは決して悪い意味ではなくて「再生材をそれだけうまく使いこなせている」ってことなんです。
例えば「こういう色目の問題なら、この素材を添加剤に入れれば解決できる」とか、そういうノウハウがあるんです。多分ものすごく研究されたんだと思いますし、我々も進化するごみ袋の水準に合ったペレットをお届けできるように工夫しています。
もちろん、開発時には失敗もありました。我々もメッシュサイズの自主規格を変更したりとか、トレーサビリティを辿って、この業者の原料は大阪和田化学さんに合わないなとか、そういう試行錯誤の結果、お互いに歩み寄れたのかなと思います。それがもしかしたら今の進化するごみ袋の製品化に繋がったんじゃないかなと。
ーなるほど。加工先の技術が要求されるものなんですね。
はい。やっぱり日本のもの作りってすごく水準が高いので、ごみ袋にするにしても、例えば顕微鏡みたいなものでコンタミ(異物)の数をみて規定数以上だったら駄目だとか、あとは毎回全部のフレコンバッグからサンプルを抽出して、機械にかけて圧力を加えて異物を検出する昇圧試験っていうのをやるところもあります。
そんな中で、大阪和田化学さんはとても柔軟だと思います。やっぱりポストコンシューマ材、つまり色々な所から集めてきた再生素材ですから、色目ひとつとっても多少のブレがありますが、それに対して例えば乳白色の着色剤をこのくらい入れようとか、色々なアイディアを持っていらっしゃいます。
そもそもの開発に至る流れも、一般的なHDPE(海外製は炭カル入りもあり)のシャカシャカしたごみ袋よりも廃ストレッチフィルムは伸縮性があるからごみ袋として使いやすい、とか、そういう他社とは違う着目点のもと、さまざまな課題を工夫して乗り越えて製品化してくださったのだと思っています。
ーありがとうございました。