企業経営にもサステナビリティが本格的に求められる昨今。時代に先駆けて環境対策と経営の両立を図ってきたのが、日本電気硝子株式会社(以下NEG)です。まだ「サステナブル経営」という言葉さえなかった1970年代からコストを惜しまず技術開発に挑み、成果を積み上げてきました。
NEGは現在、「2050年までにカーボンニュートラル達成」という目標を掲げ、精力的に活動しています。常務執行役員プロセス技術本部長の金谷仁氏と環境部長の大橋伸夫氏に、具体的な取り組みについてお話をうかがいました。
カーボンニュートラルを推進する技術力の源泉
—まずは「特殊ガラス」について教えてください。どんなものに使われているのでしょうか。
身近なところだと、薄型テレビのディスプレイやパソコンのモニター、IH・ガス調理器のトッププレートなどがあります。その他にも、医療機器や半導体、インターネット通信に用いる光ファイバ、人工衛星などにも使用されています。
「ガラスは硬くて重いもの」というのが一般的な認識だと思いますが、私たちが製造している特殊ガラスは非常に薄くてフィルムのようにペラペラだったり、糸のように細く加工できたりするのが特徴です。
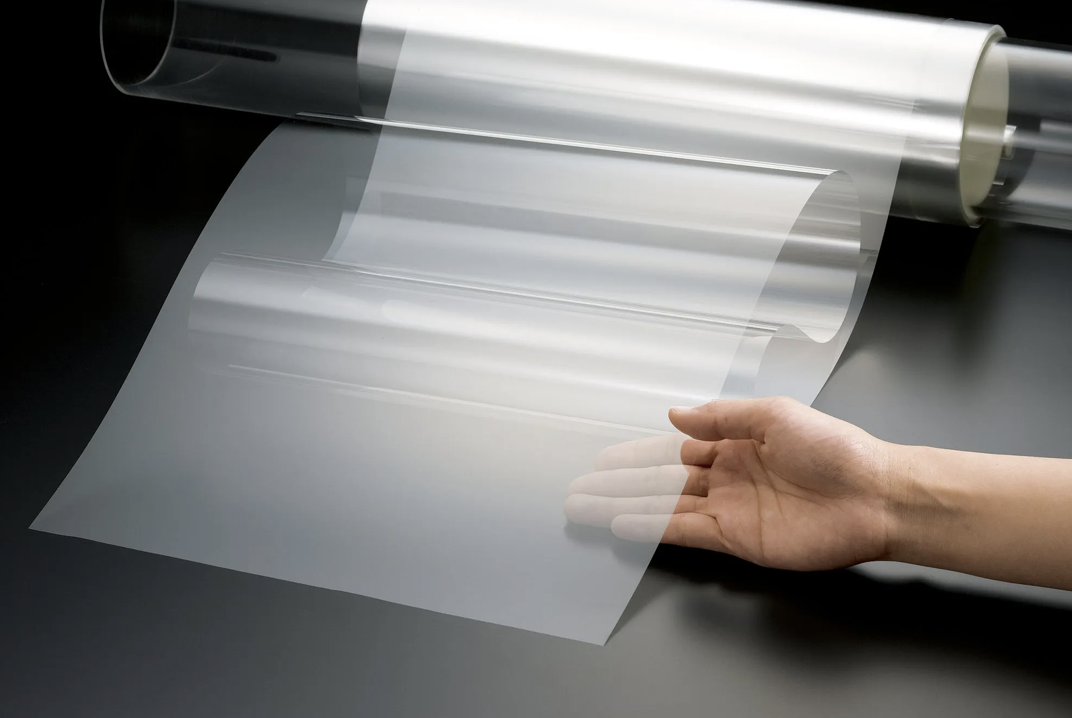
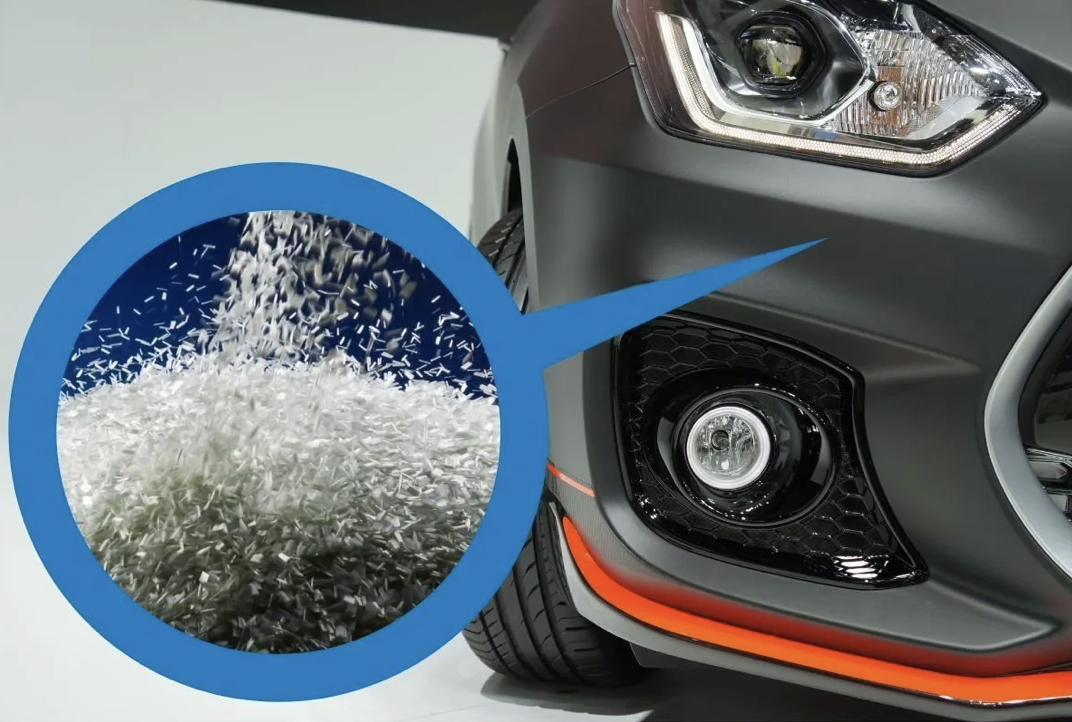
折り曲げられるガラスはスマホのディスプレイに、細く加工された糸状のガラスは自動車部品やコンクリートの補強剤として建築資材に使われるなど、社会の様々なところに使用されています。
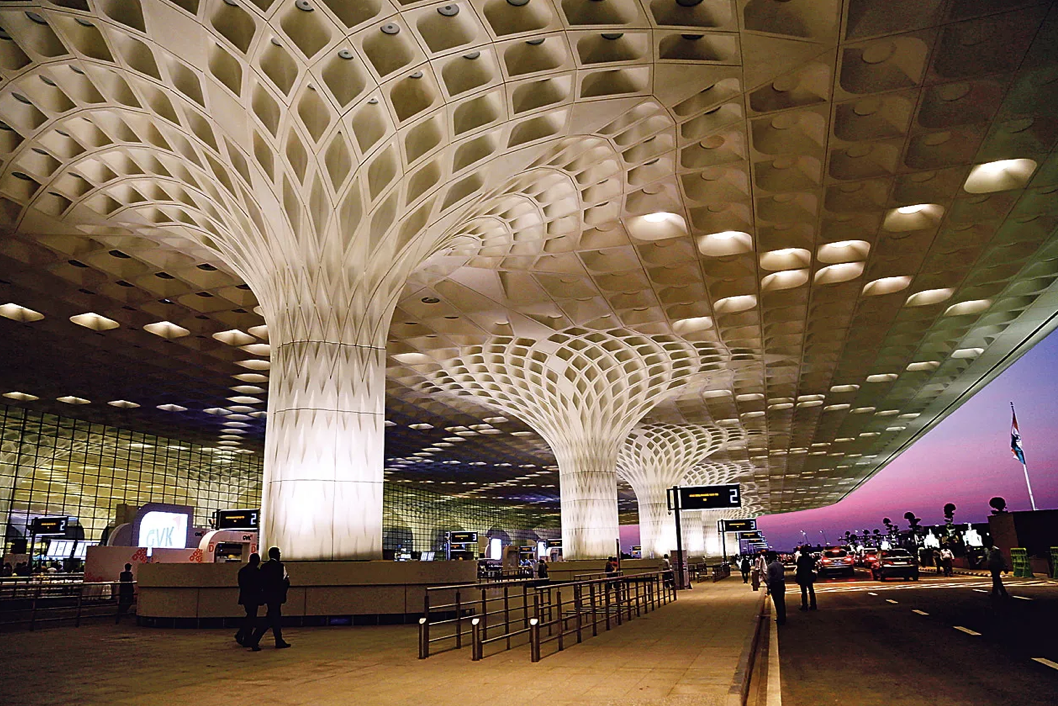
—知らないだけで、私たちの暮らしの至るところにあるのですね。ガラス製造には多くのエネルギーが必要となりますが、NEGは1970年代とかなり早い段階から「サステナブル経営」に取り組んでいたそうですね。
はい。むしろ、エネルギーを多く使うから、「サステナブルな技術」に注目してきたとも言えると思います。私たちは、「エネルギーを無駄なく生産する=インプットミニマム」というテーマを追い求めてきました。
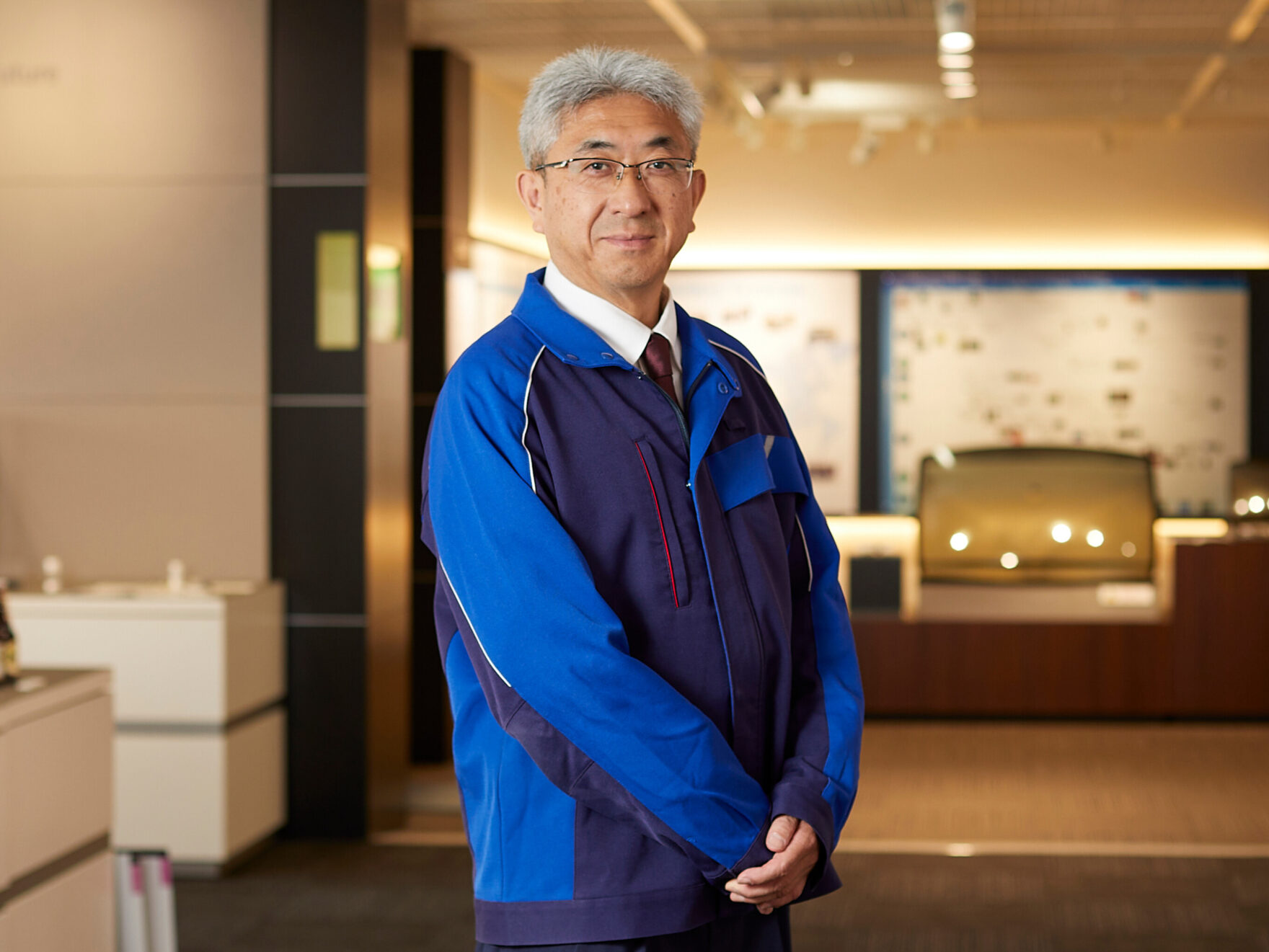
少ないエネルギーでガラス製造ができれば、環境面に貢献できるだけでなく、コストカットにもつながります。そうすれば自然と、競争力も上がっていくわけです。そのための設備や技術の投資については、短期的なコストにとらわれずに進めていくというのが、会社の方針でした。
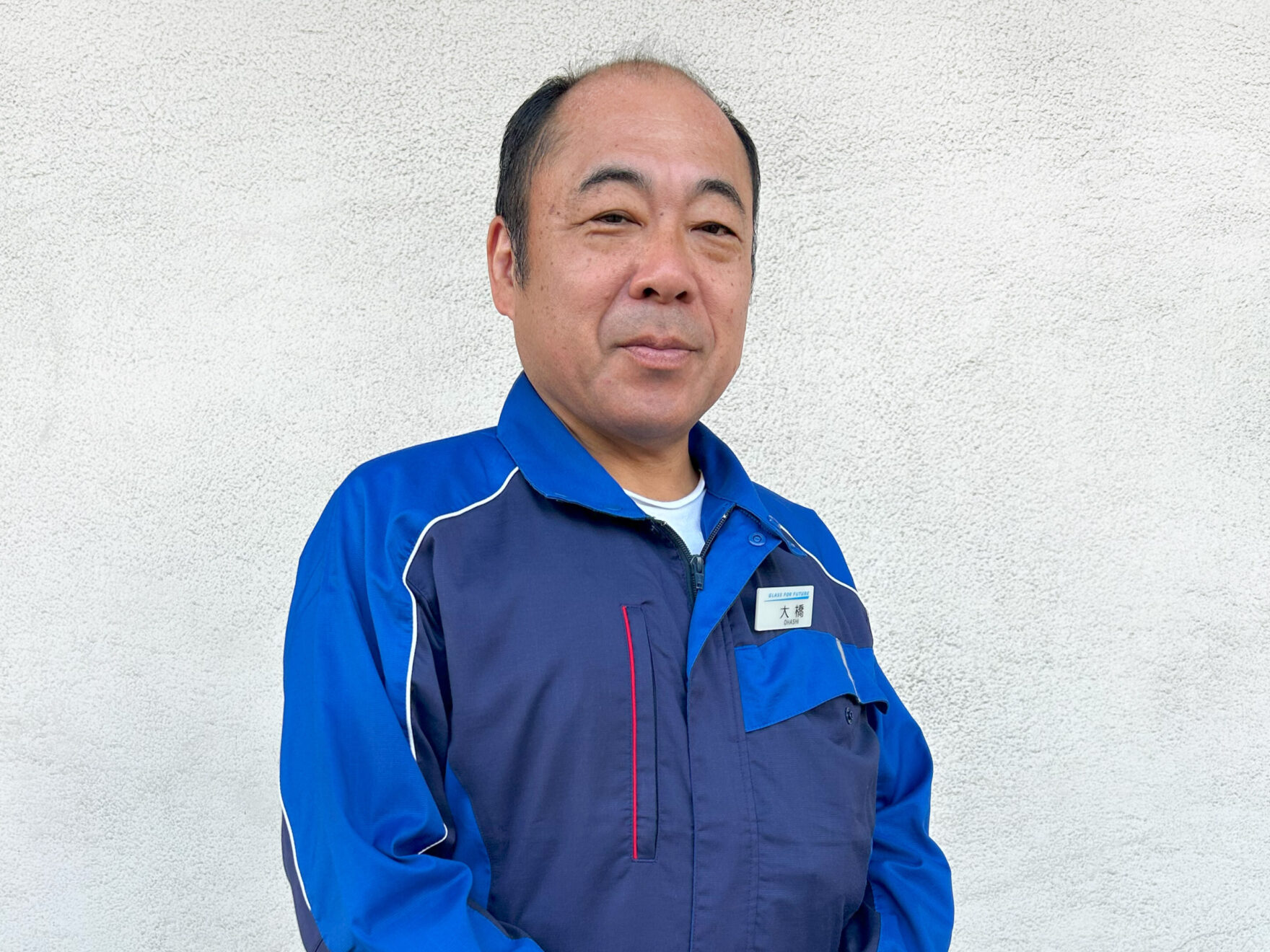
「インプットミニマム」を実現するための研究開発に時間やコストをかけても、それが必ず品質向上とコストカットにつながる。社会で環境や持続可能性に注目が集まる以前から変わらず、そうした強い思いで取り組んでいます。
業界をリードするCO₂排出削減技術
—「2050年までにカーボンニュートラルを達成」という目標のために、具体的にどのような取り組みをしているのでしょうか。
製造面で最もエネルギーを必要とするのが、原料を溶かしてガラスを作る「溶融」の工程です。したがって、ここでのエネルギー効率の向上とCO₂排出量の削減が重要となり、NEGでは大きく二つの柱で動いてきました。
一つ目が、原料を溶融するのに必要なエネルギーをすべて電気でまかなう、「全電気溶融炉」の導入。もう一つは、ガス燃焼と電気を組み合わせる「ハイブリッド炉」の電融比率を上げることです。ちなみに、ハイブリッド炉は電融比率約50%以上、それ以下は電気ブースティング炉と呼びます。
全電気溶融炉は、文字通り電気のみで溶融を行う方法で、非常にエネルギー効率が高い特徴があります。溶融を行うと排ガスが発生してエネルギーロスが生じますが、それらも最小限です。もちろん燃焼によるCO2排出量はゼロとなります。
【全電気溶融炉とハイブリッド炉の環境面での比較表】
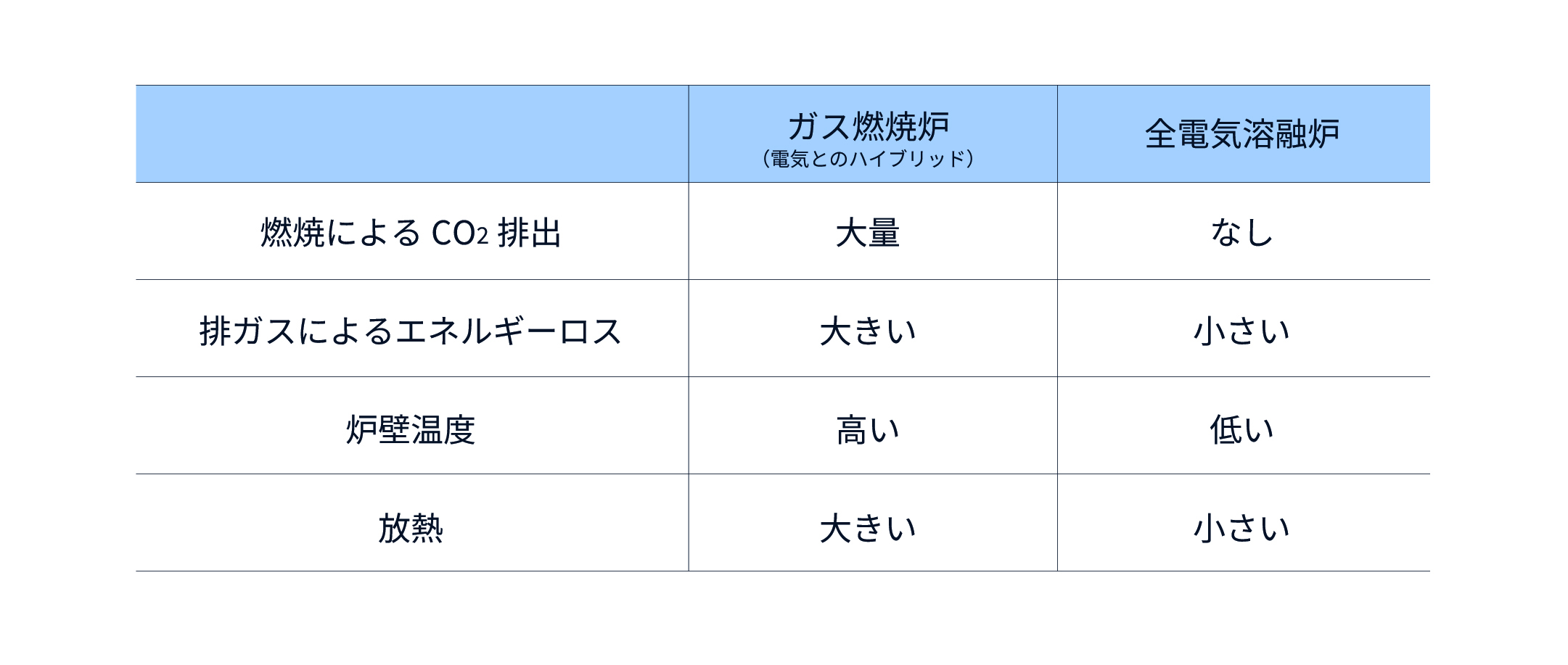
NEGが全電気溶融炉の開発に成功し、初めて導入したのは1974年で、国内ではかなり早期でした。ただ、全電気溶融炉に適する特殊ガラスの種類を増やしていくことが難しく、なかなか広げられない状況が続きました。
ですから、長らくは電気ブースティング炉(電融比率約50%以下の炉)での製造が中心でしたが、2015年頃に薄型ディスプレイ用の特殊ガラス製造で全電気溶融炉が導入できたことをきっかけに、急速に技術が発展しました。2024年現在、NEG全体での全電気溶融炉の割合は約4割(38%)まで増加しています。これは、業界的にはかなり進んでいる数字です。
今後は早期に全電気溶融炉への切り替えを図ることで、カーボンニュートラルを着実に進めたいと考えています。将来的にはすべての製品を全電気溶融炉で製造できるのが理想ですが、現時点ではまだその見通しが立っているとまでは言えません。ハイブリッド炉でしか製造できない製品が残ることも考慮し、並行してハイブリッド炉の高効率化についても進めています。
水素を使ったCO2削減技術も確立
—ハイブリッド炉では、どのような環境対策を行っていますか。
まずハイブリッド炉の説明をしますと、燃料(現在は天然ガス)を燃焼することと溶融ガラスに直接電気を流して加熱することを併用して、ガラスの溶融を行う炉のことです。
【ハイブリッド炉と全電気溶融炉の違い】
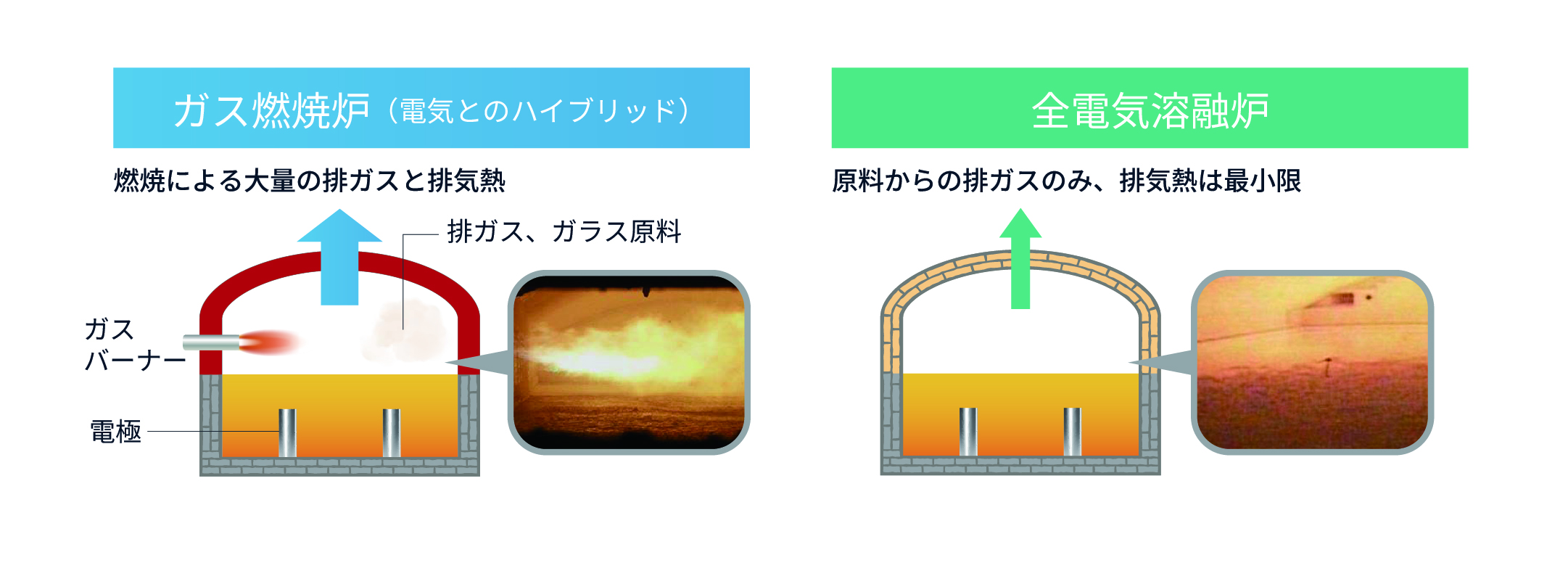
こちらも1970年代から継続して高効率化に取り組み、燃料の切り替え(重油から天然ガス)、酸素のみで燃焼する技術(酸素燃焼方式)の開発・導入、電気融比率の向上などを業界に先駆けて実現してきました。これらが、エネルギー使用量やCO2排出量の削減、さらには大気汚染物質の抑制にもつながりました。
ちなみに、酸素燃焼方式を日本で初めて導入したのは、NEGです。1993年の導入後、現在はほぼすべての燃焼炉で採用しています。また、現在稼働しているハイブリッド炉は、2010年に燃料はすべて天然ガスへと切り替え済みです。
実は、近年さらに環境面で大きく貢献できる技術の開発に成功しました。それが、天然ガスから水素への燃料転換です。
—自動車などでも注目されている水素ですか。
そうですね。2022年に水素100%を燃料としてガラスを溶融する実証実験を行い、技術的に可能となりました。水素を使用して先述の酸素燃焼を行うことにより、燃焼時のCO2排出量をゼロにすることができます。
ただ、実用化に向けてはまだ課題があり、すぐに水素を導入できる段階ではありません。コスト面に加え、ガスと比較すると水素はカロリーが非常に低く、同じ熱量を与えるためによりたくさんの容量が必要になる、という問題があります。効率面では、まだ電気には及びません。
さらに、海外に比べて日本はインフラ整備が進んでいない状態です。本格的な導入のためにはパイプラインの整備などが必要となり、NEG単体では難しいのです。こうした現状を踏まえると、今は技術を磨いて準備する段階だと捉え、社会的な状況が整えばすぐに行動に移せるよう体制を整えています。
製造過程の廃棄物はほぼ100%リサイクル
—NEGでは、生産に伴う廃棄物についても、リサイクルを徹底しているそうですね。
特殊ガラス製造の途中で排出される廃棄物は、不要なものを取り除くことさえできれば、再びガラス原料として使用できます。NEGではこれらを回収し、ほぼ100%原料として再使用しています。また、ガラス製造時には原料から排ガスが発生します。そこに粉塵が含まれているのですが、これらも回収して再利用しています。
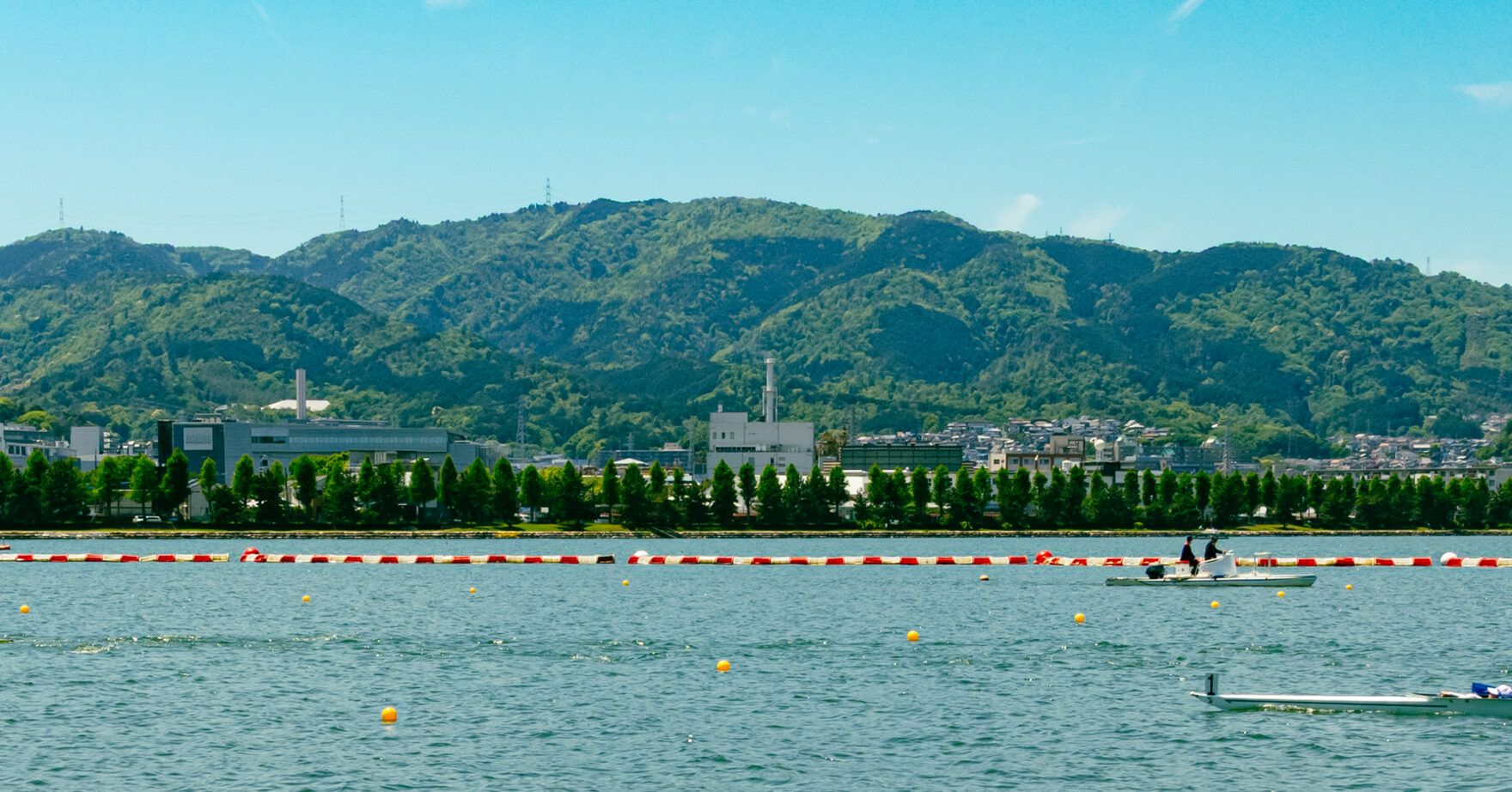
製造する特殊ガラスの種類と、リサイクル原料の相性にも考慮する必要があります。回収したリサイクル原料が同じ製品の製造には向かないケースもあるので、どんな製品なら使用できるのかをよく見極め、粘り強く試行錯誤することでリサイクル体制を確立してきました。
—こうした廃棄物リサイクルの取り組みは、業界全体としては進んでいるのでしょうか。
各企業によってばらつきがありますね。NEGの場合は、かなり先行して1970年代から取り組んできたため、原料のリサイクルが根づいています。
再生可能エネルギー導入や地域貢献も
—製造過程の環境対策のほかに、「カーボンニュートラル」に向けて取り組んでいることはありますか。
再生可能エネルギーの導入にも力を入れています。2023年には、滋賀高月事業場内に大規模な太陽光発電設備(年間約3.7GWh想定)を設置し、稼働しています。
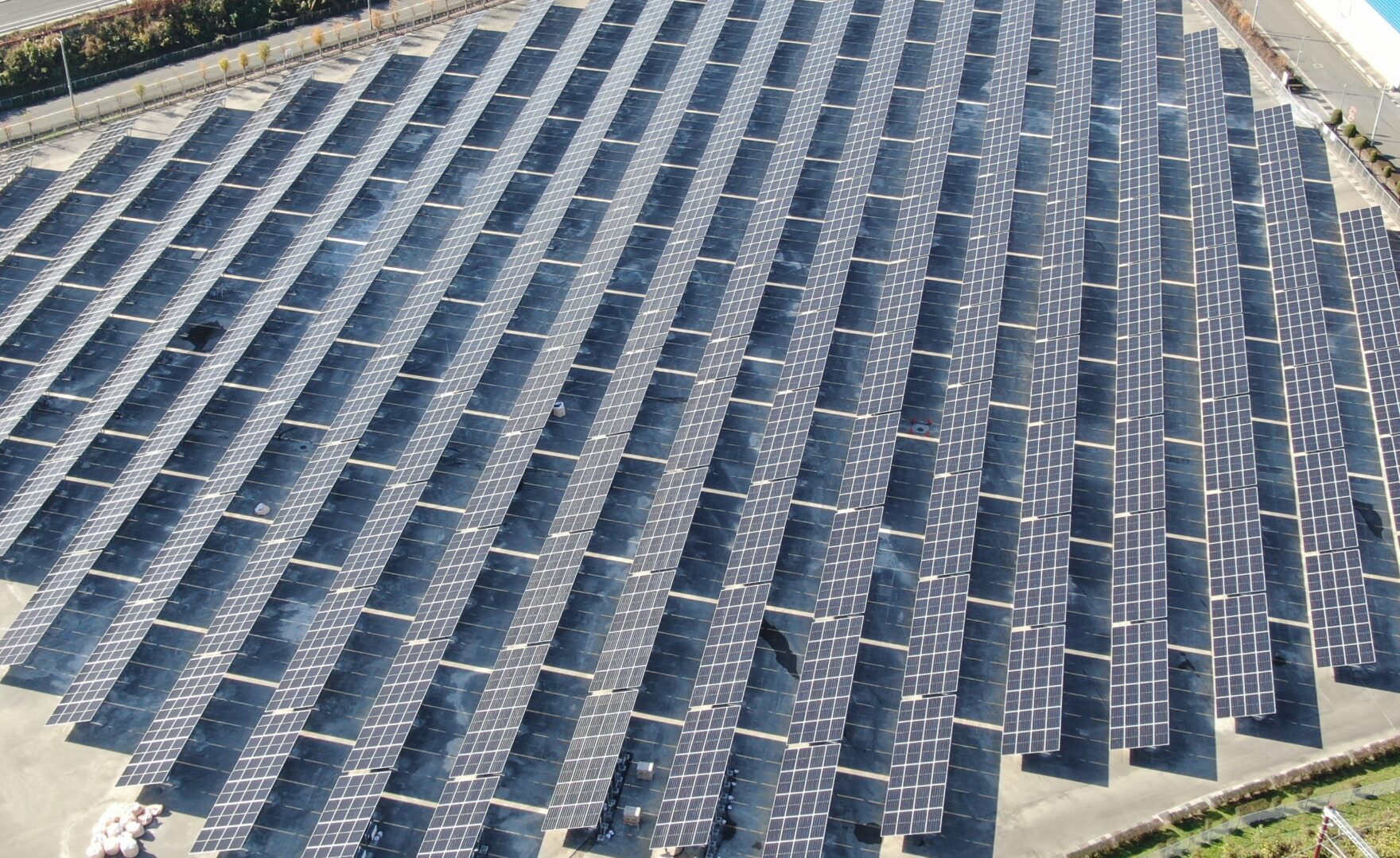
その他にも、再生可能エネルギー電力発電事業者とVPPA(Virtual Power Purchase Agreement: 仮想電力購入契約)を締結することで、環境価値の調達によるCO2排出量削減にも取り組んでいます。
また、NEGは地域の環境保全のために様々な取り組みを行っています。その一つが地元の森林組合からの継続的なJ-クレジット購入です。2018年から継続購入し、収益は地元の森林保全に役立てられています。
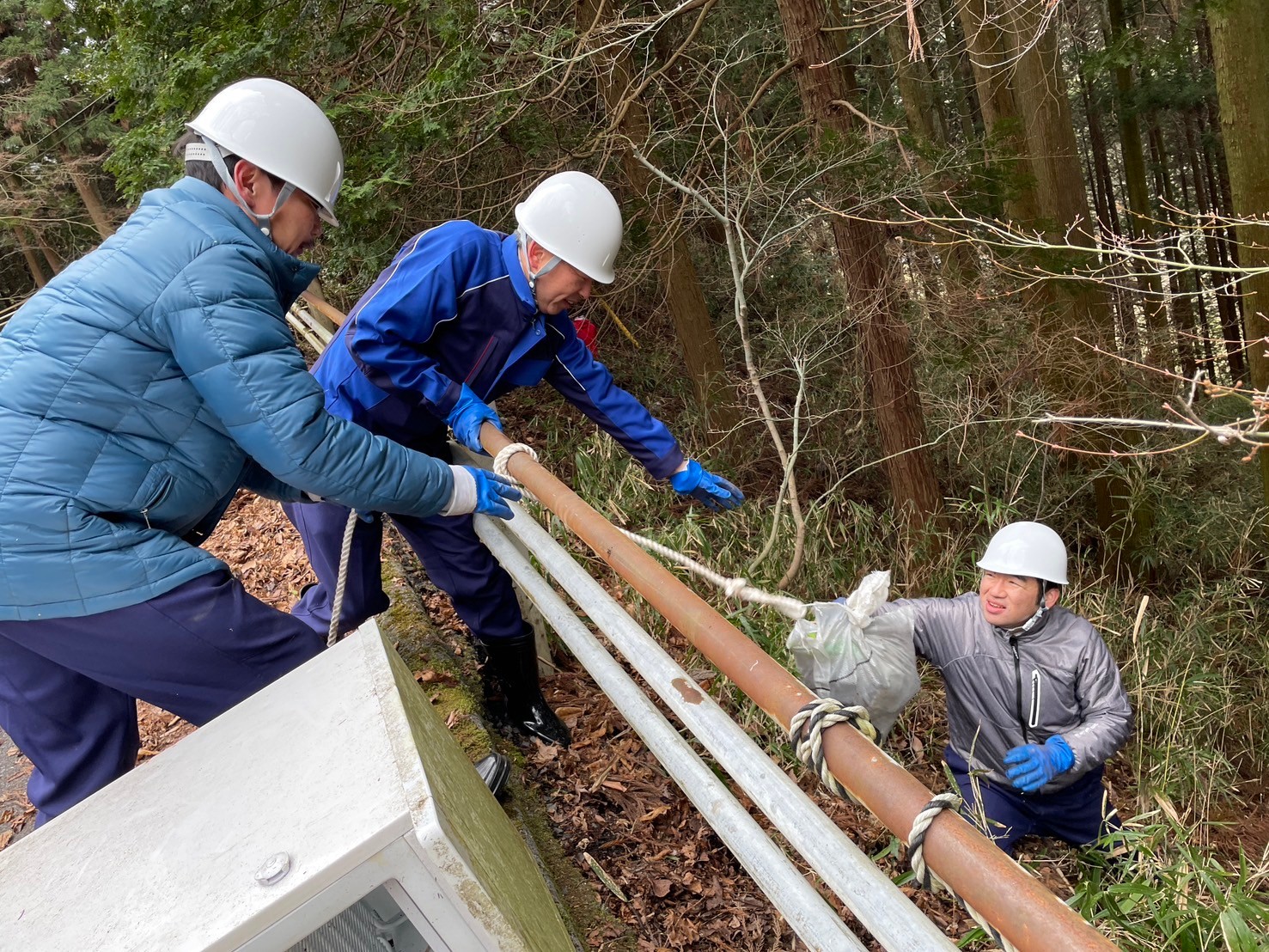
サステナブル社会に向けて更なる貢献へ
—長い時間をかけて取り組まれてきた成果が、現在の「サステナブル経営」につながっていることがよくわかりました。今後の展望についても教えてください。
製造過程のエネルギー効率を高めることも重要ですが、同時に、特殊ガラス自体が社会のサステナビリティを支え、リードすることができると考えています。冒頭でも触れた糸状のガラス(ガラスファイバ)は自動車の軽量化に寄与し、燃費の向上や生産工程の簡素化による省コストを実現しています。
また、今回ご説明した製造面での環境技術を他社へ提供する、「エンジニアリング事業」も2024年から開始しました。私たちの酸素燃焼や全電気溶融の技術は、ガラス業界のカーボンニュートラルを推進する上で重要な役割を果たすと考えています。
ガラス産業全体を見ると、CO2排出削減の取り組みに差があるのも事実です。今後はますます持続可能な製造方法が求められますから、私たちが長年蓄積してきた技術やノウハウを提供することで、業界全体をサステナブルな方向へと牽引・貢献していきたいです。
(画像はすべてNEGによる提供)